In 1913, Ford launched the assembly line to great success on one basic premise: Never stop churnin ’em out.
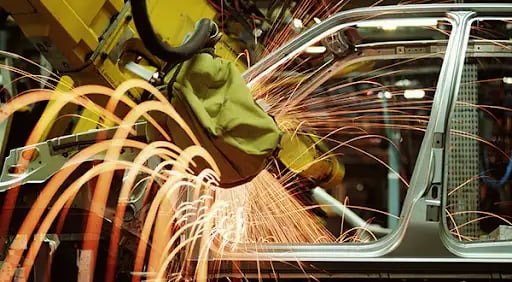
Unfortunately, the past year has highlighted the line’s fatal flaw: If even a single screw is out of stock, everything has to be turned off.
First, a brief history lesson
With just-in-time manufacturing, supplies show up just as needed to save on space and costs.
Just-in-time manufacturing developed over decades:
- 1920s: Ford mined its own iron which it then used to build cars, but the company later shifted toward outsourcing suppliers
- 1950s: Toyota executive Taiichi Ohno went to an American supermarket, saw how items were restocked as needed, and tried to replicate the process for cars
- Present day: Companies from all sorts of industries — auto firms, Apple, McDonald’s, and Target — use just-in-time to save on costs
It’s a great system for when things go as planned.
Problem is, nothing seems to be going as planned
In the last few months, the auto world has taken one helluva beating:
- The Texas snow debacle closed a refinery that produces 85% of US resins, used to make seat cushions. Toyota paused several plants as a result
- A March fire at Japanese chip manufacturer Renesas — which supplies ⅔ of the industry — sliced production capacities
Ford, for example, could see a 50% production hit and miss out on $2.5B in profits.
Companies are working to improve by stockpiling inventory, building vertically integrated supply chains, and, in the case of Tesla, signing exclusive deals for access to raw materials.
If anything, this whole ordeal has been a stark reminder for the auto biz not to put all their eggs in one basket.